Complex forming of hybrid structures

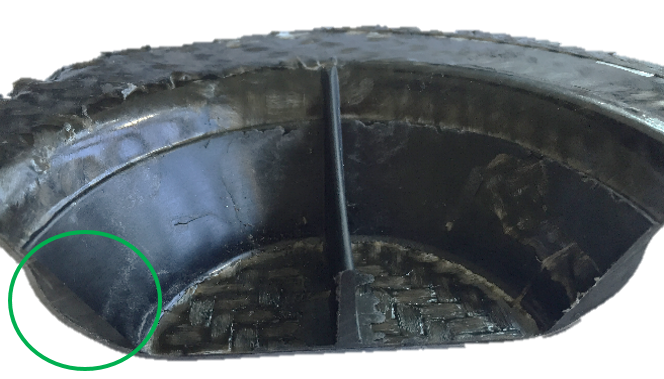
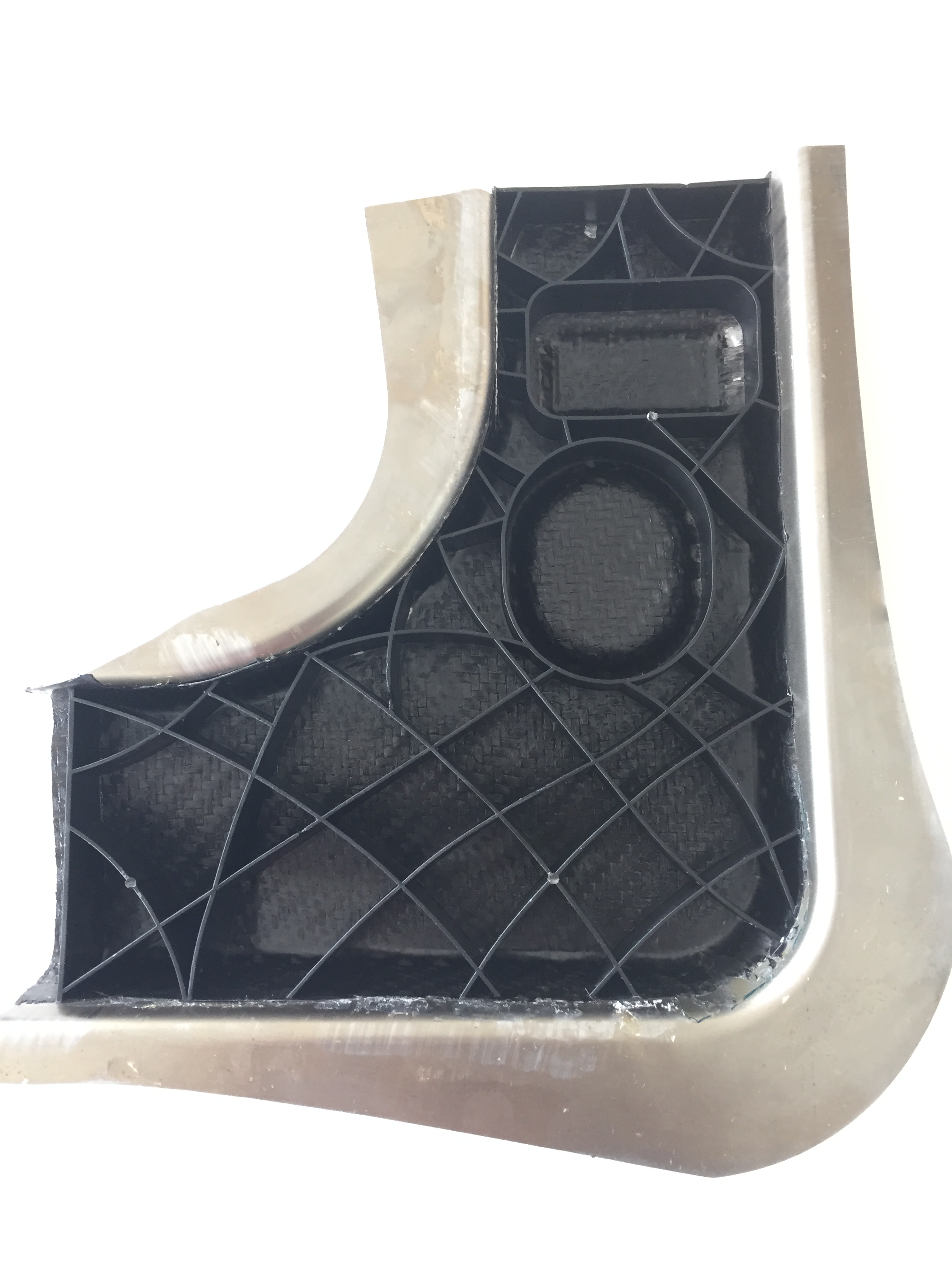
The project deals with the production of hybrid components made of metal and fiber-reinforced plastic composite (FRP) by forming and injection molding in one tool. The aim is to reduce process stages and reduce the manufacturing costs of hybrid components.
In the classic automotive mass production lightweight components in multi-material design have been no significant role. The main reason lies in the complex and therefore expensive production through a large number of individual production steps.
In the project "Complex Forming of Hybrid Structures", a technology for forming fiber composite metal hybrid components is being redeveloped. The aim is to efficiently combine the processes sheet metal forming, joining, fiber composite pressing and injection molding.
The main objective of "KomuPlex" is the appropriate integration of the FRP component into the forming process of the metallic component in order to reduce the depth of the process level of FRP hybrid components and to increase the degree of integration. The generated partial undercuts result in a positive connection of metal, organic sheet and plastic. The project results lead to a new one-tool technology.
Main focuses of the project:
- Tests with simple cup tool
- Component construction of a pillar shoe
- Tool development and production
- Process chain for the production of the hybrid components
- Demonstrator production
- Component characterization
Project results:
- Preliminary tests successfully implemented
- Tool put into operation
- Demonstrator components manufactured using the on-tool process
- Component cycle (without preheating) around 80 seconds
- Partial deformation represented by plastic melt